FORKLIFT TINES
Fork-Co stocks standard ITA/FEM Forklift Tines in Class II, III, and IV in our facility in Alvin, Texas.
- Stock lengths from 32 inches to 144 inches
- Fully Tapered and Polished Tines
- Pin Type Tines
- All forklift tines are forged, shot-blasted and machined to meet ISO standards
- Our manufacturing facility can modify and customize to meet needs
LINKS:
Standard ITA/FEM Hook Type Class II (View Details)Standard ITA/FEM Hook Type Class III, IV (View Details)
Fully Tapered Forks Class II, III, IV (View Details)
Pin Type Forks, Special Mounting and Shapes (View Details)
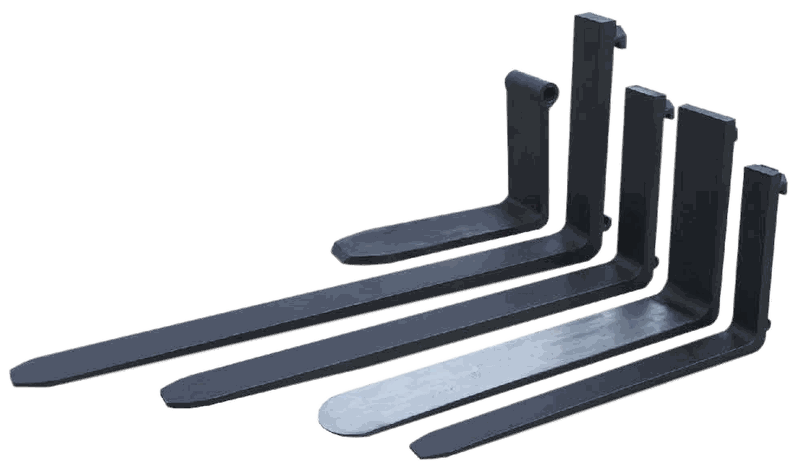
What to know about Forklift Tines...
Forklift Tines are one of those common components of industry that for some reason manages to allude us in establishment of common vocabulary. Referred to in different circles as forks, forklift tines, forklift blades, forklift teeth, etc. they are essentially the load bearing components on the front of standard configuration forklifts. Not only can we in the industry not come to a singular mind on what to call Forklift Tines, outside of the ITA/FEM Standard for Hook Type Forks (sometimes called Pin Type Forks) we have yet to see a standardization of design in how to affix the forks to the front of a Forklift and any number of other dimensions of the ever-so-simple, yet ever-so-complex forklift fork. The Following is an attempt to provide a reference for the layman in selecting and ordering new or replacement forks:
ITA Hook Type Forklift Tines:
Hook-ITA fork classes are the same world -wide under ISO standards. The standard FEM hook style forklift tines come in two types, “A’ & “B”. The difference in the types reflect differences in the ground-to-carriage distance when the mast id fully lowered. Type “A” is primarily used for indoor and many outdoor trucks. Type “B” is primarily intended for outdoor trucks. However, the applications can be interchangeable. Type “B” forks can replace type “A” forks, but not vice-versa because the type “A” would not reach the ground.
In North America, classes are designated by Roman numerals. The rest of the world uses Arabic numbers.
Hook Tine Classes:
Class I is forklifts up to 1,999 LB at 24” load center
Class II is forklifts rated 2,000 LB through 5,500 LB @ 24” load center
Class III is forklifts rated 6,000 LB to 10,000 LB @ 24” load center
Class IV is forklifts rated 10,000 LB to 17,500 LB @ 24” load center
Class V is forklifts rated from 17,500 LB to 24,000 LB at 24” load center
If unsure, measure the carriage height from top edge to bottom edge:
Class I: 13”
Class II: 16”
Class III: 20”
Class IV: 25”
Class V: 28.67”
Under-Clearance by type:
Class I a 3” Class I b 4.5”
Class II a 3” Class II b 6”
Class III a 3” Class III b 8”
Class IV a 5” Class IV b 10”
Class V a 5” Class V b 10.12”
Rough terrain trucks will possibly have higher under-clearance, but not always.
High Under-Clearance Tines:
Popular in many Euro and Asian brand trucks since many of those are standard with solid “pneumatic” tires so they can be indoor-outdoor trucks.
Pin Type Tines:
Pin type forks have no standard shape or size. They vary from OEM to OEM and by trucks within a brand. Because of this we ask many questions of customers. We use 2 drawings to gain dimensional data needed to make the forks to fit. These tell us where the fork tubes are located. The most important dimension is the location of the tube center in relation to the rear face of the tine shank. This dimension tells us the “offset” or “inset” of the tube, or whether it is “in-line.”
In relation to the rear face of the fork shank, offset means the tube center is located toward the driver. Inset means the tube center is located toward the load. In line means the center is directly above the rear face.
Piggy-Back Forklift Tines:
There is a type of forklift that is mounted on the rear of trailers and is carried to building sites to unload the flatbed. These are called “piggy-back” forklifts.
Block or Brick Forklift Tines:
Block Forks are narrow forks, usually used in multiples, that enter the openings of concrete blocks that are turned on their sides. A layer of these blocks is used as the actual load carrying pallet in unit loads of blocks.
Lumber or Plywood Forklift Tines:
Lumber Forklift Tines or Full-Tapered Forklift Tines or Full-Taper and Polished Forklift tines are made with a typical maximum thickness of 1.5 inches and in various widths, depending on the load weight. They are all made as full bottom taper forks, meaning the taper runs from the tip , back to approx. 2 inches from the bend. The top of the forklift tine is polished, unpainted, for ease of entry and exit. Tips are thin with a top chamfer for chiseling between plywood sheets and the tips are squared off, not rounded, to assist the chiseling effort. When these forks become very wide, they can block the driver’s visibility. Therefore, a “peek-a-boo” forklift tine is used. This fork has a shank that is thicker than the blade. At a certain distance above ground level the shank narrows to allow the driver better visibility.
Gypsum Forklift Tines:
Gypsum Forklift Tines are forks having a tall shank that extends very high above the top hook. To this shank, a synthetic covering, usually replaceable, is added.
Coil Forklift Tines:
Coil Forklift Tines are used to handle steel or other coiled materials. These tines made with the top corners of the blades chamfered or radiused to prevent scoring or denting of the inner layers. When both forks are used together in the core, only the top outer corners need this shape. If each fork is used to handle one coil each, then both top corners of the fork are chamfered.
Kiss Forklift Tines:
Kiss Forklift Tines are used to handle coils and are made with a bend in the lower shank. The bend shapes the fork shank so that even though the shanks are separated, they offset toward each other so that the blades “kiss” each other. The tines are then used in the core of the coil. The reason for this offset is that the center vertical support bar of the pin type carriage on which they are used does not allow the forks to touch. The standard width from outside to outside of the forks when fully closed down may be too wide for the core.
Tire Forklift Tines:
Tire Forklift Tines are tines having a full length bevel along the inner face of the fork. This bevel is used to allow the tines to slide under the tread of a tire or stack of tires for damage prevention and stability during handling. Tire forklift tines have a blunt tip and no bottom taper.
Folding Forklift Tines:
Folding Forklift Tines fold up against the shank. They are used to shorten the overall length of a forklift. Uses could be in space restricted areas like elevators, or on forklifts that are transported on the platforms built onto the rear of flatbed trailers. Minimum thickness of these forks is 2 inches and they are mostly in class II or III hook configurations.
Spark Retardant Forklift Tines:
Spark retardant Forklift Tines are used in hazardous operations where spark-proof forklifts are used or where sparks may caused combustion/explosion. These tines are brass coated both on the blade and the face and sides of the shank. The brass is usually 1/8” thick and perhaps a little thicker on the bottom for wear resistance. The brass cladding is a weldment made to fit tightly onto the tine. It is not removable. Stainless steel cladding can be used for applications where sanitary requirements are prevalent: Pharmaceutical, Beverage, food processing, where the fork is exposed to the product in the manufacturing process.
Drum Forks:
Drum forklift tines are tines having the inside of the blade radiused to match the wall of a standard steel 55 gallon drum. This design is used on tine positioners and pallet fork clamps. These cut-out tines can be configured as one cut-out on each fork to handle single drums or two drums side by side, or two cut-outs per fork to handle two drums or four drums. The thickness of these tines should be increased due to a loss of capacity caused by the radius cuts.
Fork-Co Leads the Pack
With our industry best lead times (4-5 weeks on complex builds), full in-house engineering and design team, on-site manufacturing and fabrication facility just south of Houston, TX, and very large standard product inventory, Fork-Co is the right choice for your project. We stand behind our products 100%, either it accomplishes your goals, or we aren't done.
To install this Web App in your iPhone/iPad press
and then Add to Home Screen.